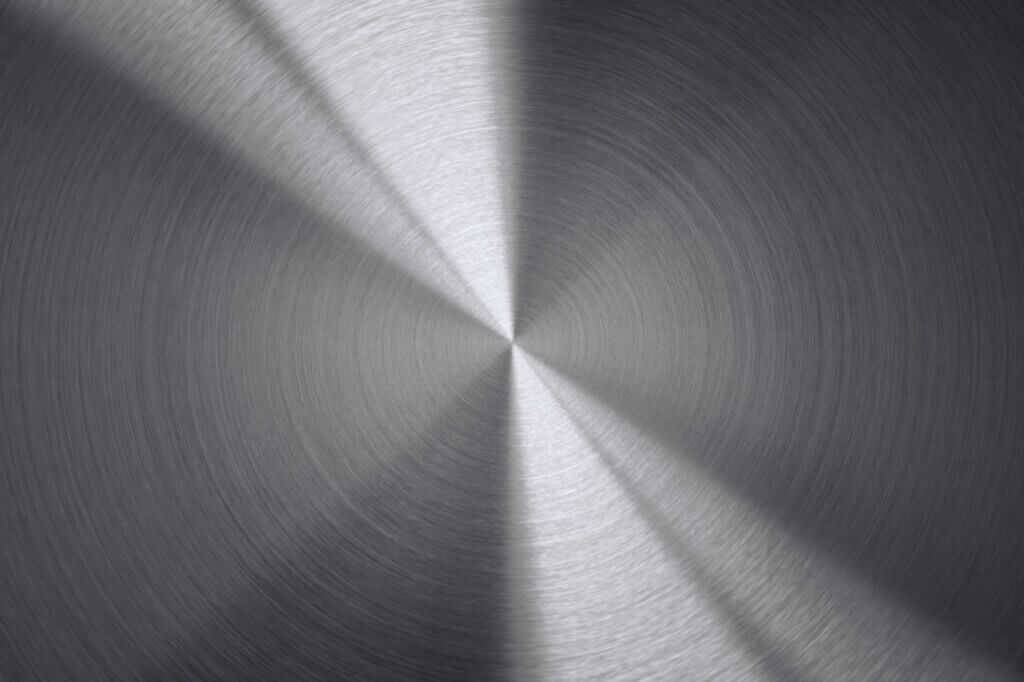
When it comes to a high-quality, corrosion-resistant product, consistency is key. This means that the entire stainless steel production process must be planned and controlled to perfection.
First, the raw materials are melted together in an electric arc furnace. This can take between 8 and 12 hours of intense heat. Steelmakers then add chromium and other alloys to achieve the exact chemical composition desired.
Melting
The raw steel materials are melted in an electric furnace. This step typically takes 8 to 12 hours and is very precise in terms of temperature. During this process, excess carbon is removed by processing the molten metal through an argon-oxygen decarburization converter. This helps create more austenitic alloys with better stress corrosion resistance in chloride environments.
Once the molten steel has been refined to exactly the desired chemical composition, it’s then cast into semi-finished forms such as blooms (rectangular shapes), billets, slabs, rod rounds, or tubes. The next stage is hot rolling, which happens at a temperature above the alloy’s recrystallization point. This step reduces the thickness of the material while giving it a more finished appearance.
In addition to this, many of the mechanical testing procedures that are carried out help determine how well the stainless steel can resist impacts, pressures, and strains. The tensile and toughness tests are the most commonly performed.
Refining
The mix of iron and other elements that comprise stainless steel is crucial to its resistance to specific corrosives. Differing proportions of these elements – chromium, nickel and molybdenum, in particular – affect the strength of the protective oxide layer and how resistant it is to stress corrosion cracking.
To fine-tune the molten mix, the alloy is decarbonized and homogenized. This process takes place through either argon oxygen decarburization or vacuum oxygen decarburization, which injects an argon gas mixture or evacuates the steel in a vacuum chamber to reduce carbon content while balancing and honing its temperature and composition.
The now-pure stainless steel is cast into temporary forms. These might take the form of slabs, rods, tubes or blooms (cuboids). During this phase, mechanical tests are used to determine the steel’s physical properties, including its tensile and toughness. These tests are carried out to ensure that the material meets and exceeds its grade requirements.
Casting
Once the raw materials are ready, they’re melted together in an electric furnace. This typically takes between 8 and 12 hours of intense heat. The resulting molten steel is cast into semi-finished forms like blooms (rectangular shapes), billets, slabs, rods and tube rounds. These are the building blocks of wrought stainless steel products, which will be turned into finished products at other factories.
Unlike regular iron, the addition of chromium makes stainless steel resistant to corrosion. The chromium creates a passive surface layer that protects from oxygen and moisture.
The casting process also allows for a lot of geometrically complex parts to be made. This is particularly important for high-performance applications such as automotive exhaust systems and industrial equipment. During this stage, the metal goes through mechanical testing and chemical analysis to ensure it meets quality standards. DATAMYTE lets you conduct layered process audits to identify and address potential quality issues early.
Hot-Rolling
After the alloy is melted, it’s cast into temporary forms — either slabs, blooms (rectangular shapes), billets (square or circular cylinders), and rods. This step requires a great deal of precise temperature control, as the molten steel must remain above its recrystallization point to avoid sticking when passed through hot rollers.
This is the final process before the stainless steel can be used to make products. The material’s chemical and mechanical properties are tested again, including tensile and toughness tests that assess its ability to resist impacts and strains.
The resulting stainless steel must go through an annealing treatment to relieve internal stress and soften it. This process varies by grade, but may include a combination of controlled heating and cooling to improve its strength or resistance to corrosion. It is also descaled and prepared for further processing.
Heat-Treating
The stainless steel alloy is made from a combination of iron and chromium. It can also contain other elements like nickel, silicon and nitrogen in varying amounts that affect properties such as ductility, strength and resistance to specific corrosives.
This combination of materials is melted together in an electric furnace. It typically takes about 8 to 12 hours for the material to completely melt. Once the molten metal is ready, it’s cast into temporary forms such as slabs, blooms (rectangular shapes), billets and rods. These can be used as raw materials for forming wrought stainless steel products.
As these semi-finished pieces go through a number of manufacturing steps, they tend to accumulate an unwanted coating of carbon and chromium oxide known as “furnace scale.” This scale isn’t just unattractive; it can impact corrosion and stain-resistance. The removal of this coating is called descaling and involves heating and cooling the steel to create a passive surface film.
Annealing
The last step in stainless steel production is annealing, which involves giving the metal controlled heating and cooling to relieve internal stress. This can help to ensure that the finished product will be strong and durable. It can also help to prevent distortion and rusting by making the metal easier to shape.
The steel is melted in an electric arc furnace, with carbon electrodes contacting recycled scrap and alloy additions of nickel, molybdenum and other elements. Once molten, the material is cast into ingots or continuous casting to make slabs and billets. Some of the materials undergo hot-rolling to reduce their thickness into sheets or strip, while others are drawn into smaller diameters to create rod and wire.
If the steel is rolled to thin thicknesses, it must be annealed to reset its properties before it can be used. This process allows atoms to migrate within the steel microstructure to resolve dislocations and re-crystallize the grains. This re-crystallization helps to restore the workability and ductility that was lost through the rolling process.