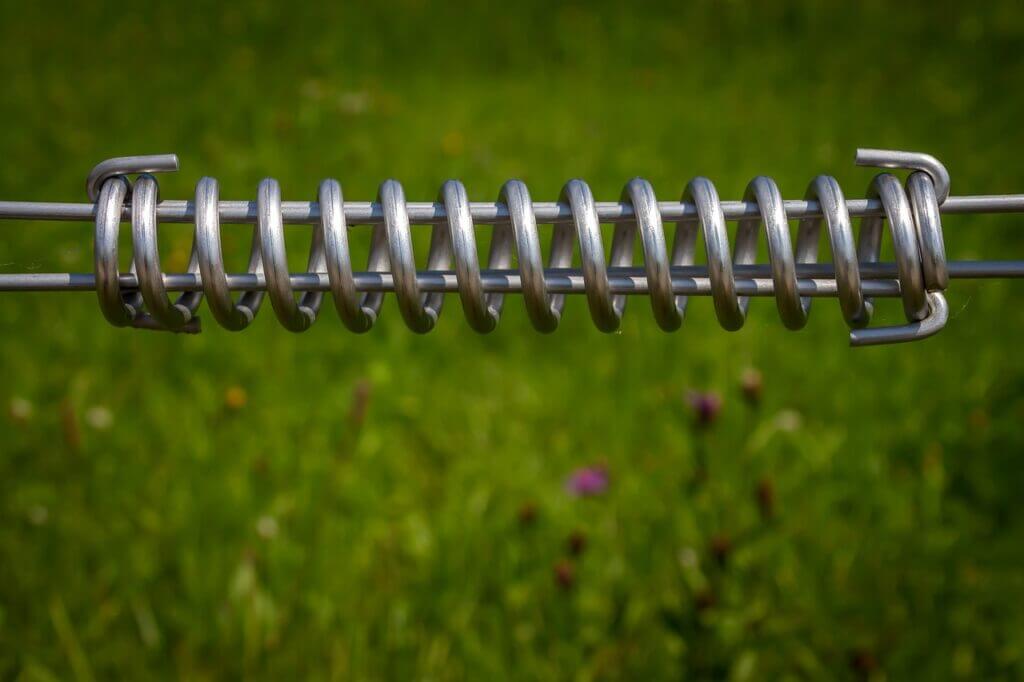
Image Source: Pixabay
Powder coating is a durable finish that can be applied to a variety of metal products. It’s used on everything from auto parts to furniture. It can be applied to any metal object that can hold the electrostatic charge used to affix the sprayed powder and tolerate high temperatures during curing.
What is Powder Coating?
Metal is the material of choice for manufacturing a wide variety of products, from household items to industrial machinery. Its durability, strength and abrasion resistance are key advantages over other materials, but it is also susceptible to corrosion and oxidation. Powder coating provides a durable, rock-hard finish that protects metal from weather and physical impact. It is cheaper, more energy- efficient and less toxic than liquid paint, reducing operating costs for businesses. It requires minimal operator training and supervision, which helps reduce workplace injuries and housekeeping problems. It also requires fewer hazardous chemicals than conventional painting, making it safer for employees and the environment.
Powder coating is an electrostatic process that involves free-flowing dry powder ionized to cling to grounded work pieces. The powder particles are charged using an electrostatic gun and accelerated toward the grounded work piece by compressed air. The powder ions react with the work piece’s surface to create an even layer of hard-wearing, weatherproof color.
Powder coating can be used on a variety of metal items, including coil springs. Other popular applications include automobiles, industrial equipment, outdoor furniture, architectural items and signs. The powder coating process is also ideal for appliances, electronics and other devices made from metals that are sensitive to heat. Powder coating can also be used on plastics, but it is not recommended for rubber or other materials that may melt.
Preparation
Powder coating is a very versatile and durable finish. Unlike spray paint that can drip and run, powder coats are evenly applied for consistent coverage. They are also very easy to clean, and abrasion resistant. However, one drawback of powder coating is the need for specialized equipment that can be expensive to purchase or rent. This can limit its use by small operations or the DIY hobbyist.
To powder coat springs, they must first be cleaned to remove any dirt, oil or grease. This process is called etching and it helps the new powder coat adhere to the metal surface. The springs are then dipped in an acid bath to prepare the surface for the powder coat.
The next step is to apply the actual powder coat. This is done by electrostatically charging the particles and then applying them to the springs in a controlled environment. Once the coat is on, it is baked in a special oven to cure it. This curing process takes place at high temperatures, often over 400 degrees. This can soften some materials, especially those used in the construction of coil springs, and cause
the center bolt to loosen or even break. This is why most spring tuners will not powder coat their work. However, if a spring is properly blasted with garnet and powder coated at 350 or less it should not effect the spring rate.
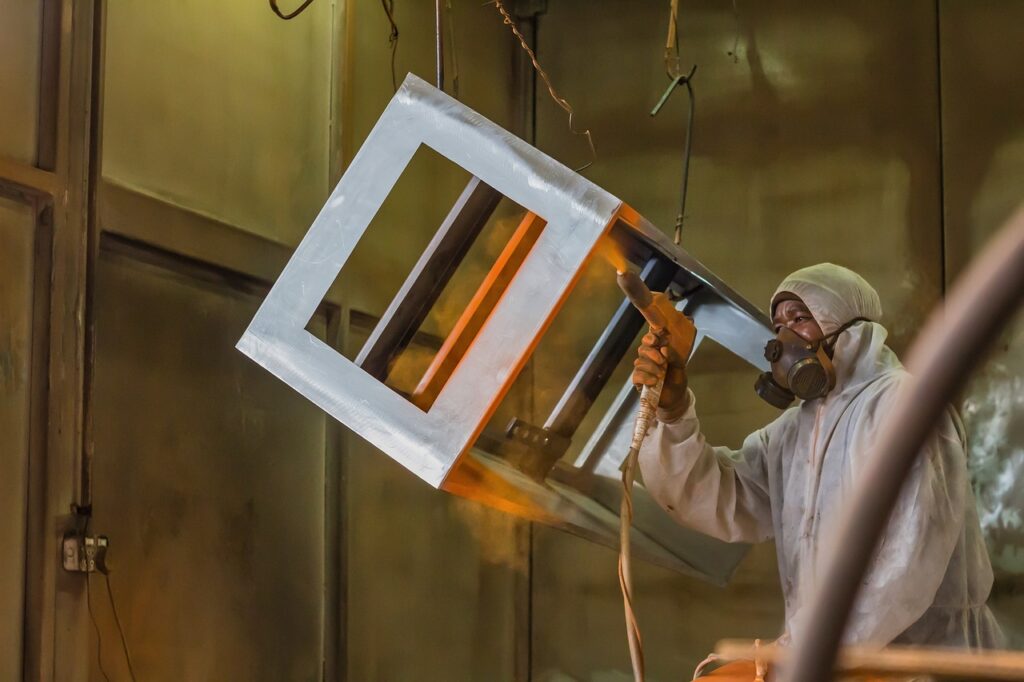
Image Source: Pixabay
Spraying
Powder coating requires a high-tech industrial oven and spray equipment. The process is often time-consuming and expensive for small operations. However, trained powder coat consultants can help improve productivity and profitability through customization and automation.
A custom system can include oscillators, reciprocators, and robots to manage the spraying and drying processes for increased efficiency. Automated gun triggering reduces downtime for maintenance and increases the utilization of the powder feed.
The first step is to sandblast the item to be coated until it is down to bare metal. Some items may also be chemically stripped with a solvent like acetone or other chemicals designed for that specific coating. This removes any grime or gunk and prepares the springs for powder coating.
A powder coating contains polymer resins, leveling agents, and pigments that are ground into a fine texture similar to flour. The dry powder is then electrostatically sprayed onto the surface of the parts with an electric charge to fuse it into place. The pieces then go into a curing oven where the heat catalyzes a chemical reaction, creating a high cross-link density within the powder that results in a highly durable finish.
Powder coatings are usually applied at temperatures between 350 and 500 degrees Fahrenheit. This heat can change the stiffness of Eibach coil springs depending on how much they are heated and for how long.
Curing
Powder coating is a great way to color your coil springs without effecting the rate. However, the spring rate will be affected by heat throughout the curing process and how much of the original powder coat remains on the springs. It is important to consult with a professional like AR Powder Coating to ensure the best results for your project.
Most metal objects can be powder coated, as long as they can hold the electrostatic charge used to affix the sprayed powder and can withstand high temperatures in the curing oven. Some examples include home appliances like mixers and gas ranges, automotive products like wheels and bodies, as well as outdoor home features and décor such as doors, lamp posts, and statues.
ESD-coated parts must be cured in a special oven, and the schedule will vary depending on part size, shape, thickness, and the required cure time and temperature. As the sprayed powder is heated to its melting point by the curing oven’s heat, it bonds with the surface of the ESD-coated material and hardens into a tough, durable protective shell.
There are a number of methods for removing a powder coating, including sandblasting and chemical strippers. The most common solvents for this job are methylene chloride and acetone, though both of these are being replaced by safer and more environmentally friendly alternatives such as benzyl alcohol and methanol.