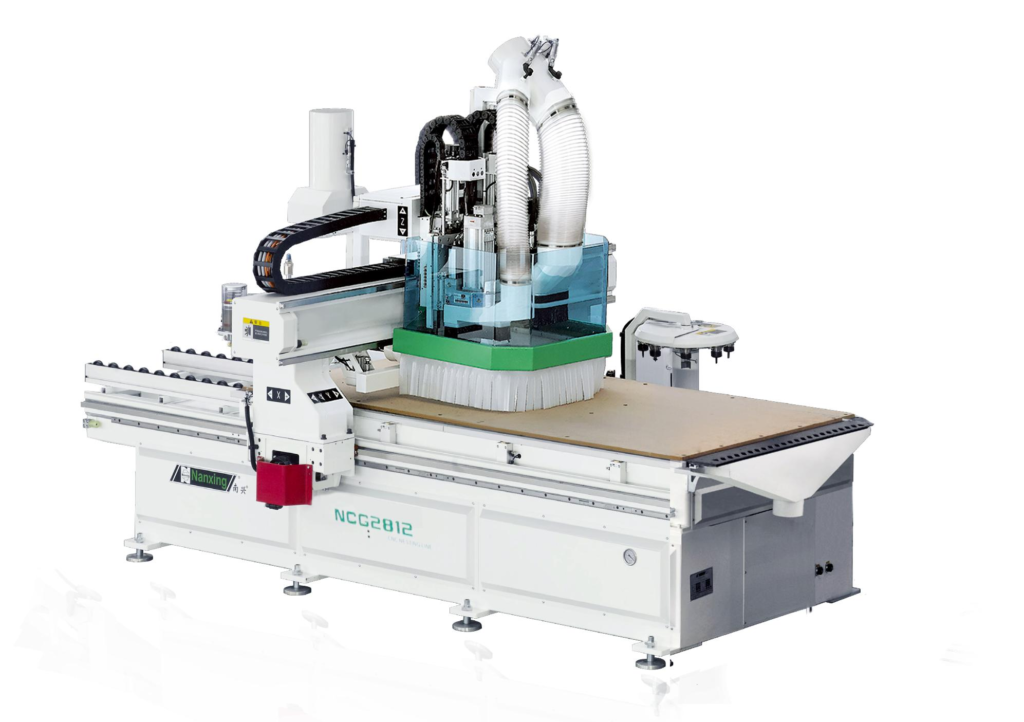
Nesting is a process that arranges parts in order to reduce material waste and save time. It also improves material utilization and increases productivity.
Good nesting software can identify common edges between adjacent parts and cut them in one pass to save time and power. This can greatly increase production efficiency and reduce labor costs.
It is a process of arranging parts on a sheet of material.
It is important to nest parts in order to reduce the amount of material waste generated during machining. This can be achieved by using specialized nesting software, which uses algorithms to determine the best way to fit parts together. This process can also help to improve productivity, as it allows you to machine more parts per sheet of material.
However, it is important to note that nesting is not always a cost-saving tool. It depends on the design of your part and the volume of production. If you have a design with very few shapes that are similar and will be cut multiple times, it may be more efficient to use manual placement instead of nesting.
A nesting file can be imported into a CAM program, which generates G-code that can operate a CNC machine to cut out the parts from the sheet of material. This allows for better control of the positioning of each part, and can avoid the possibility of two near-identical parts being mistaken for each other and incorrectly routed. In addition, SWOOD CAM 2022 offers new functionality that makes it easy to manage label positioning, ensuring that the correct parts are positioned on the board before machining begins.
Using nesting software can save a lot of time and money. It is especially helpful if you’re working with non-recyclable materials that are expensive to produce, or if you’re attempting to cut out a large number of parts. Nesting software can also be a good solution for complex designs that have many cuts and holes.
It is a process of reducing material waste.
Nesting is a process of arranging multiple parts on a sheet of material to reduce material waste and optimize finished good production. It can be used for a variety of materials, including plastic, metal, fabric, and wood. It can help manufacturers save time and money by reducing the number of cuts needed to make a product. In addition, it can help reduce the amount of waste produced during the machining process.
This process reduces the amount of material that is wasted during machining by minimizing waste and optimizing the use of raw materials. This can save companies significant amounts of money, reduce energy costs, and improve productivity. In addition, it can also help reduce the carbon footprint of a metal fabrication company by reducing the need for mining and logging.
Traditionally, nesting was done by hand using a ruler and a marker to mark out the desired cutting pattern on a blank piece of material. This can be a time-consuming and labour-intensive task. Today, nesting software is available to automate this task and eliminate the need for human intervention.
Most nesting software will either allow you to design the part within the application itself or import it from a CAD system (DXF, AutoCAD, SolidWorks, etc.). Once the pattern of parts has been arranged it will generate a cutting order and then convert it into the NC code required for the CNC machine to run. This can drastically increase your manufacturing speed and reduce the overall cost of your parts.
It is a process of reducing material costs.
Nesting is a process of arranging parts on flat material to reduce waste and maximise material utilisation during cutting or fabrication. It is a key part of lean manufacturing and can significantly reduce production costs. It reduces waste by minimizing gaps and awkward placements that would otherwise generate significant scrap materials. This is especially important when working with expensive materials, like metals. In addition, it also helps to save time and labour by avoiding the need to manually cut and machine individual parts.
Dedicated nesting software analyses the shapes and sizes of metal sheet parts to determine the best arrangement, thereby saving on material costs and increasing productivity. The software minimises gaps between the parts and utilises space, and then produces an optimised layout that can be fed to the CNC machine to cut the parts out of the sheet.
It is also possible to perform group nesting, allowing multiple parts of the same material to be grouped together on one board. This can be a useful feature when machining wooden furniture, as it allows you to match the grain direction of the different pieces. It can also be beneficial for workshops with limited storage space.
Although nesting is a useful tool for optimizing material usage, it is not the only solution for reducing production costs. Other best practices, such as maximizing tool diameter and minimizing travel distance, can help to increase efficiency and reduce costs.
It is a process of increasing productivity.
Nesting in cnc machines is a powerful tool for increasing productivity by minimizing material waste. It allows manufacturers to create more parts from a block or sheet of stock material, which can help improve production times and reduce overall costs. This technology can be used in a variety of industries, from automotive to furniture manufacturing. However, implementing nesting software can be challenging for many manufacturers. This is because the software needs to be configured according to the type of machine it will be using.
To optimize nesting, manufacturers must use specialized software that analyzes the geometry of each part and the dimensions of the stock material. It also takes into account factors like material strength and grain direction. This software can then generate a layout for the part that maximizes material utilization, minimizes waste, and reduces cutting time.
Many manufacturers are leveraging the power of nesting in cnc machines to increase productivity. This process helps them produce more parts in less time, reduce scrap and rework, and improve overall product quality. Additionally, it can save companies time and money, and allow them to focus on their core business operations. While the benefits of nesting are numerous, it is important to consider the specific needs of each company when selecting a nesting solution. For example, if an operation receives a high volume of short orders, it might be more effective to nest on a machine with a panel saw, which can cut multiple layers at once and eliminate setup.